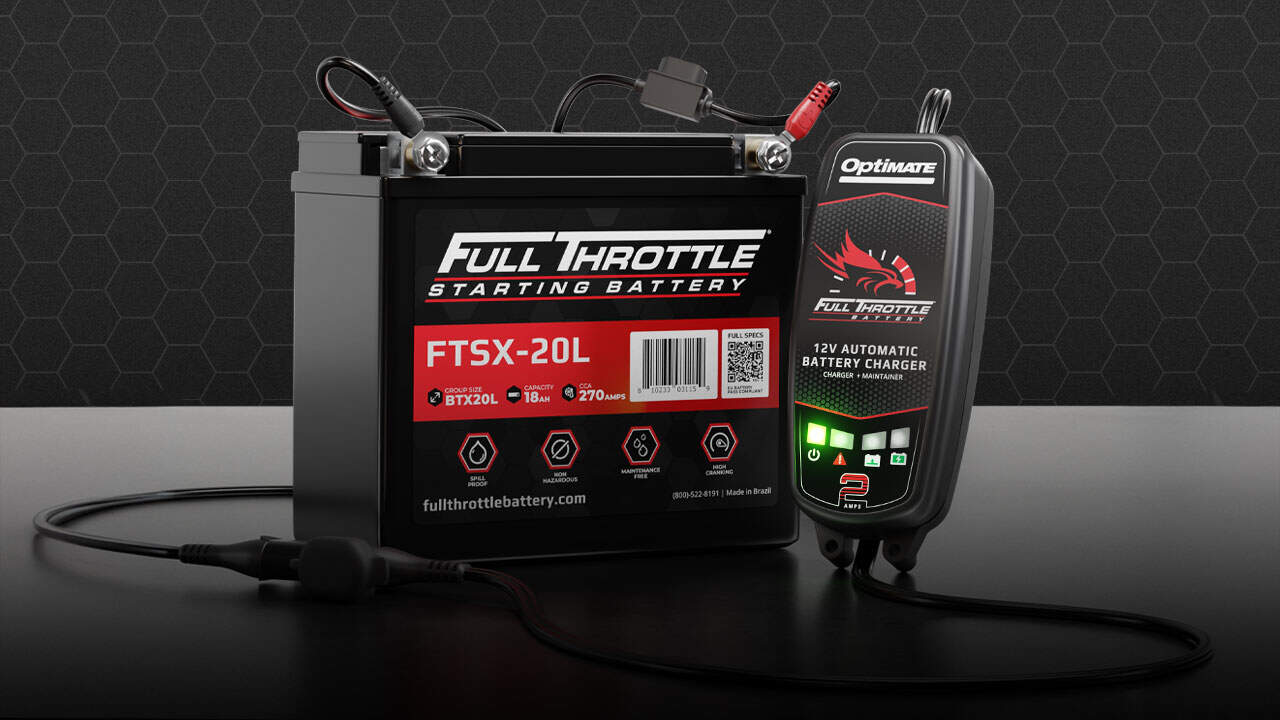
Powersport and Automotive Battery Charging: A Powerful Solution
Published: July 10, 2025
Categories: Articles
Charging batteries for powersports is one of the most misunderstood and neglected applications. Too often these misconceptions lead to early failures of batteries that potentially could have lasted many years longer if proper care had been given. Especially when dealing with AGM technology, proper charging is critical to long-life. Fullriver/Full Throttle has observed one of […]
More Industry Articles
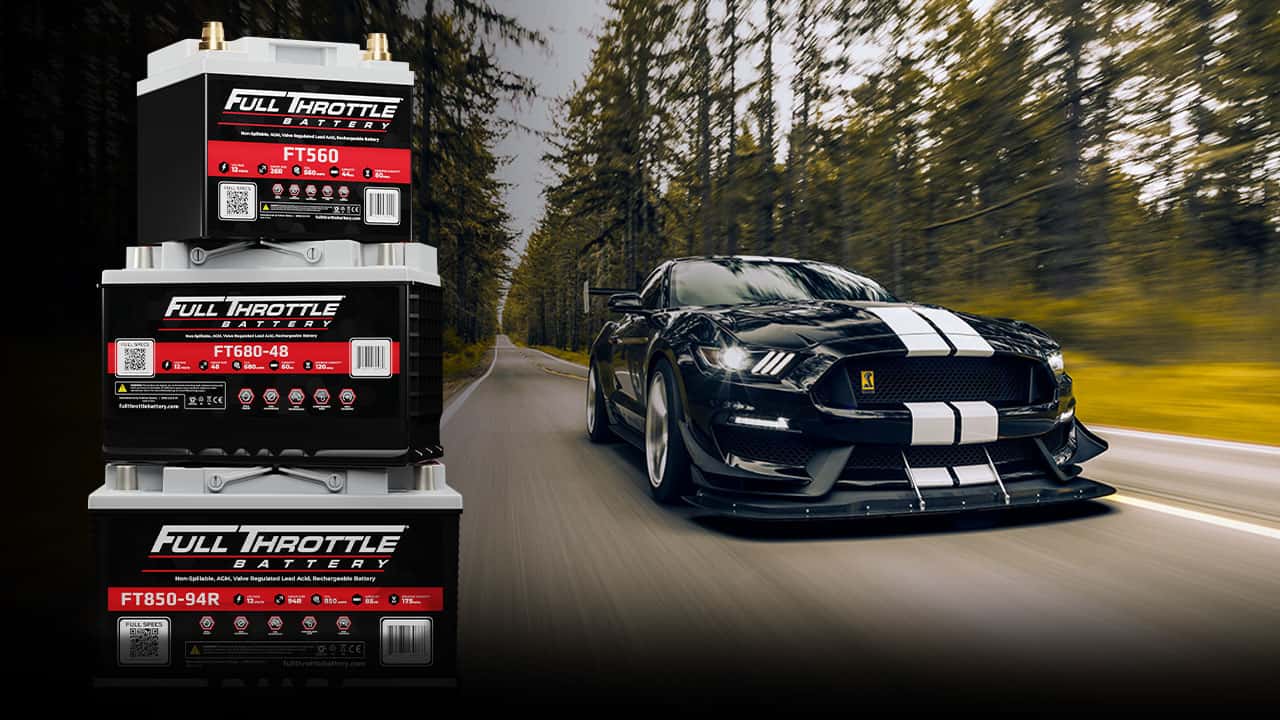
Maximizing Battery Life in High-Performance Vehicles
June 17, 2025

The Future of AGM Batteries in the Age of EVs
May 27, 2025

What is a True Deep Cycle Battery?
May 13, 2025
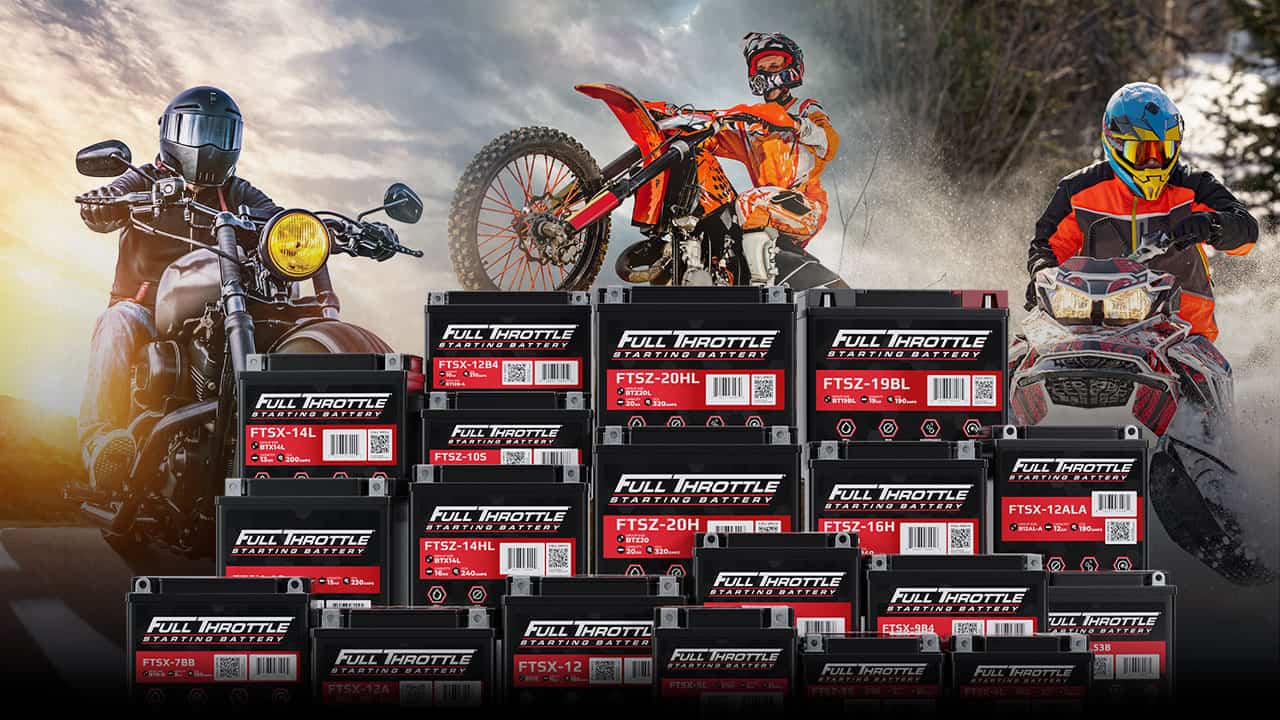
The all-new Full Throttle Starting Series!
February 26, 2025
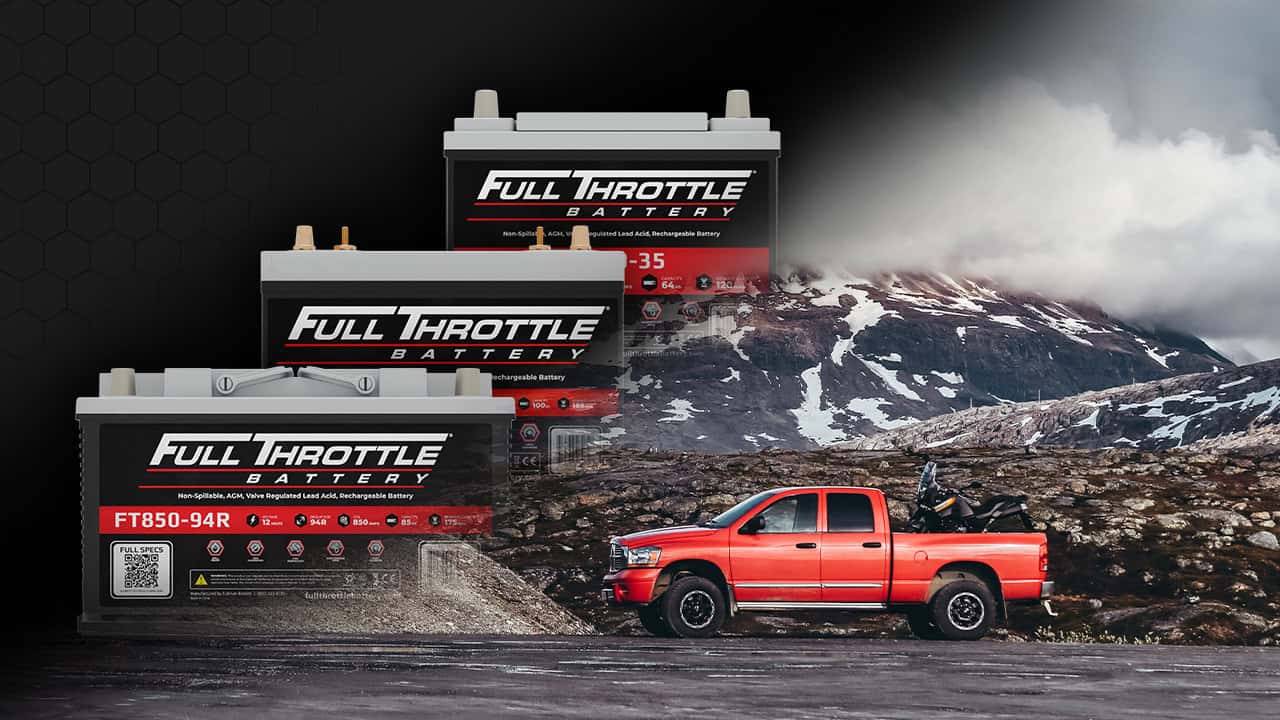
Need the perfect starting battery?
February 12, 2025
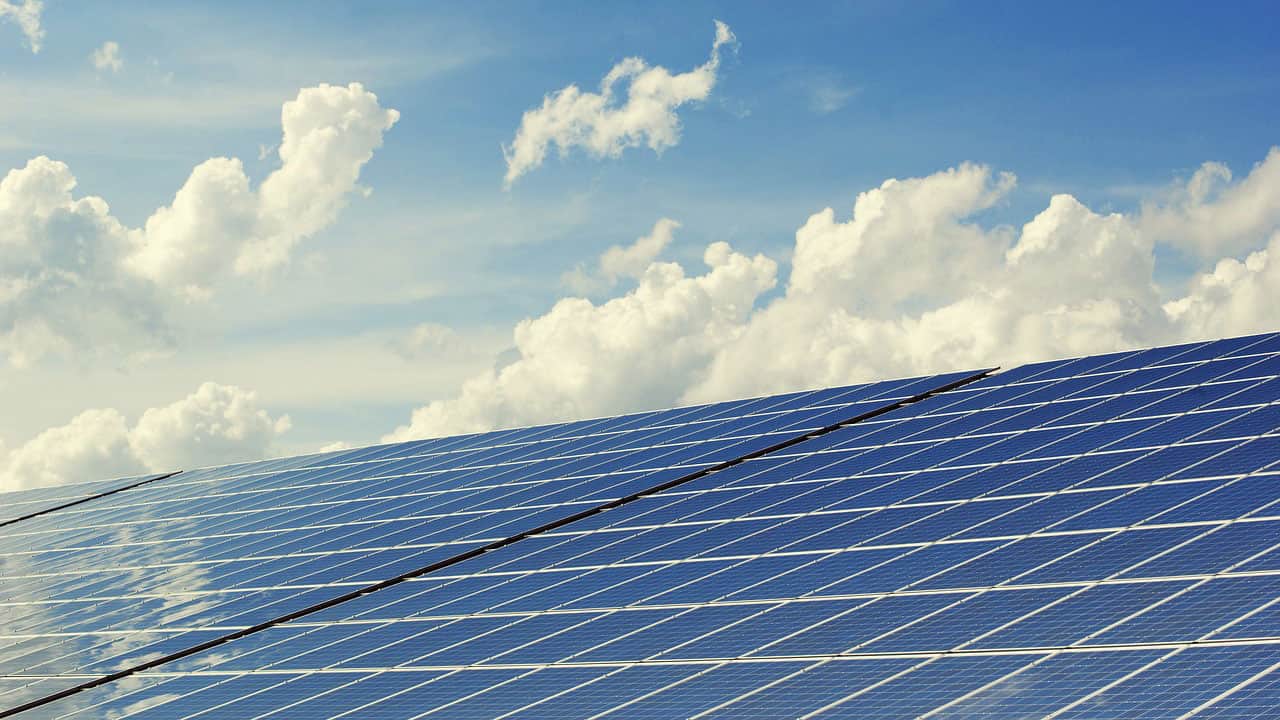
Batteries supporting renewable energy grids and Infrastructure
January 15, 2025
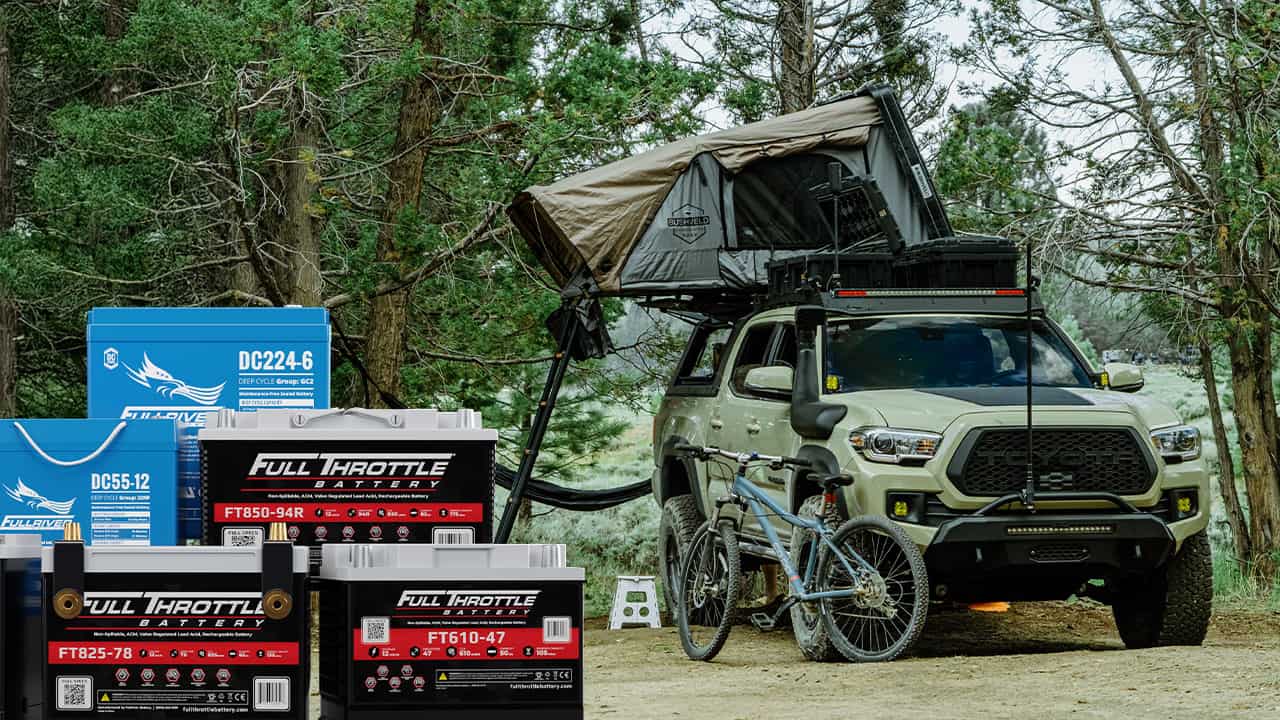
Adventures Off the Grid: Overlanding and Camping Batteries
December 24, 2024

Battery Safety 101: Common Mistakes and How to Avoid Them
December 24, 2024

AGM/GEL Battery Charger Selection
December 24, 2024
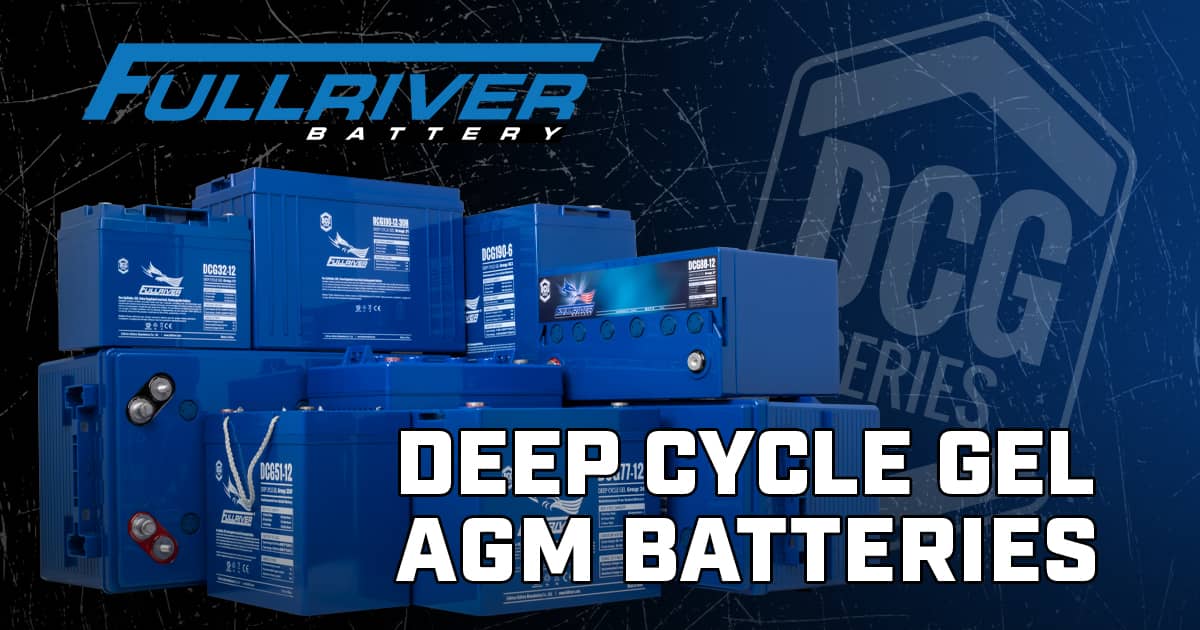
AGM vs. GEL Batteries: Which is Right for Your Application?
September 24, 2024
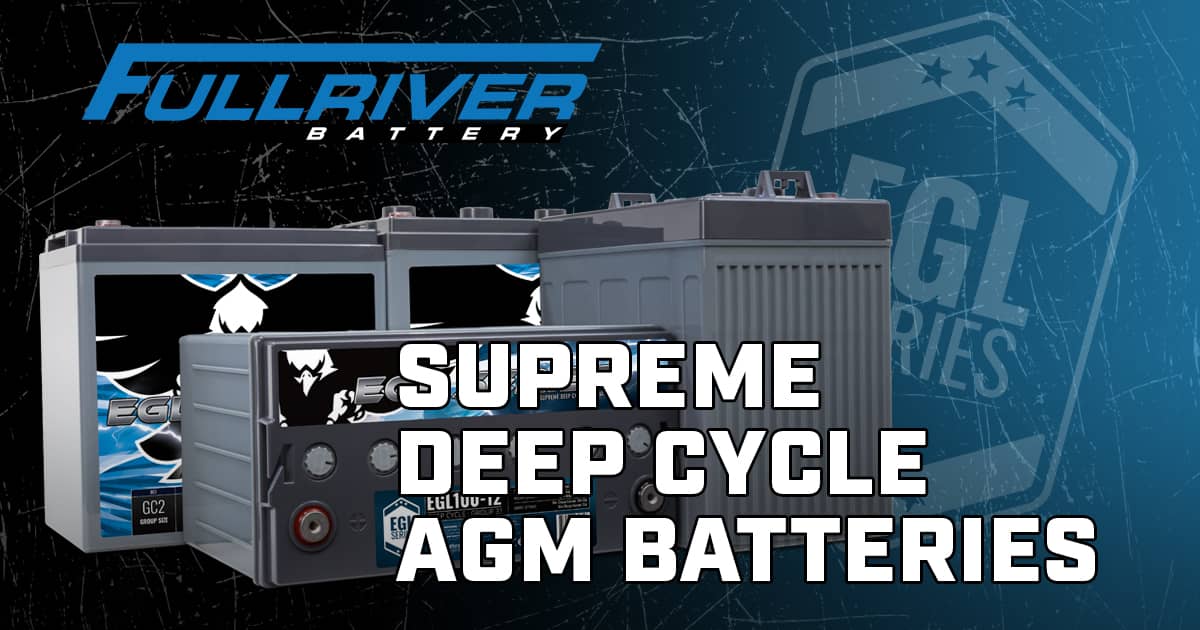
Deep Cycle Batteries as Energy Storage Systems
September 24, 2024
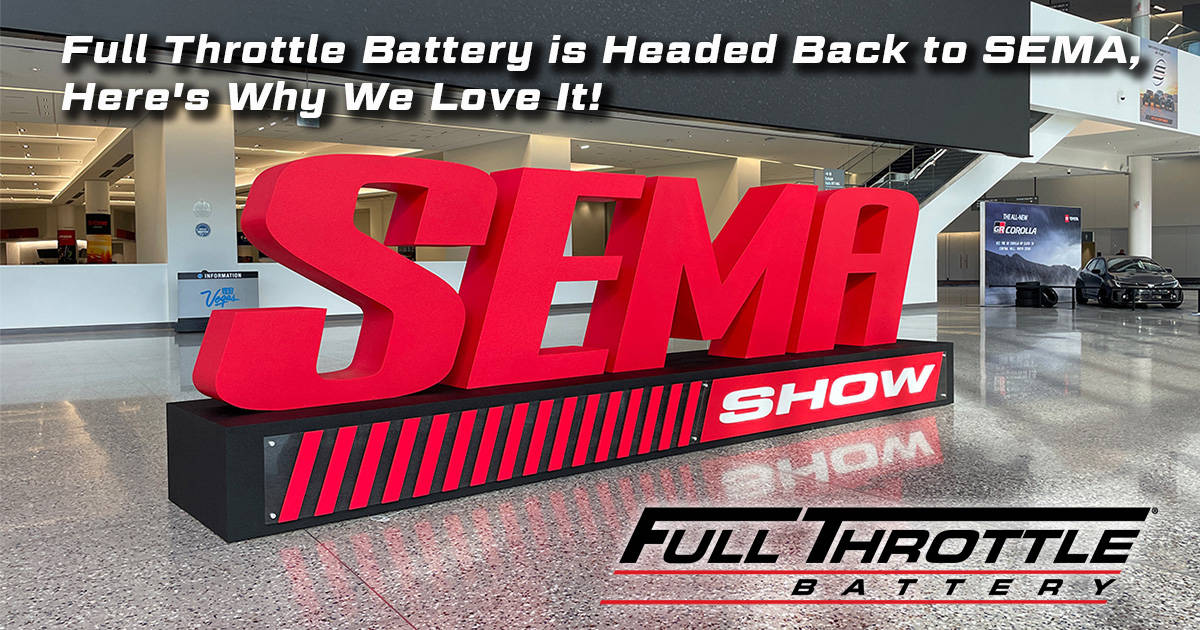
Full Throttle Battery Gears Up for SEMA 2023
October 24, 2023
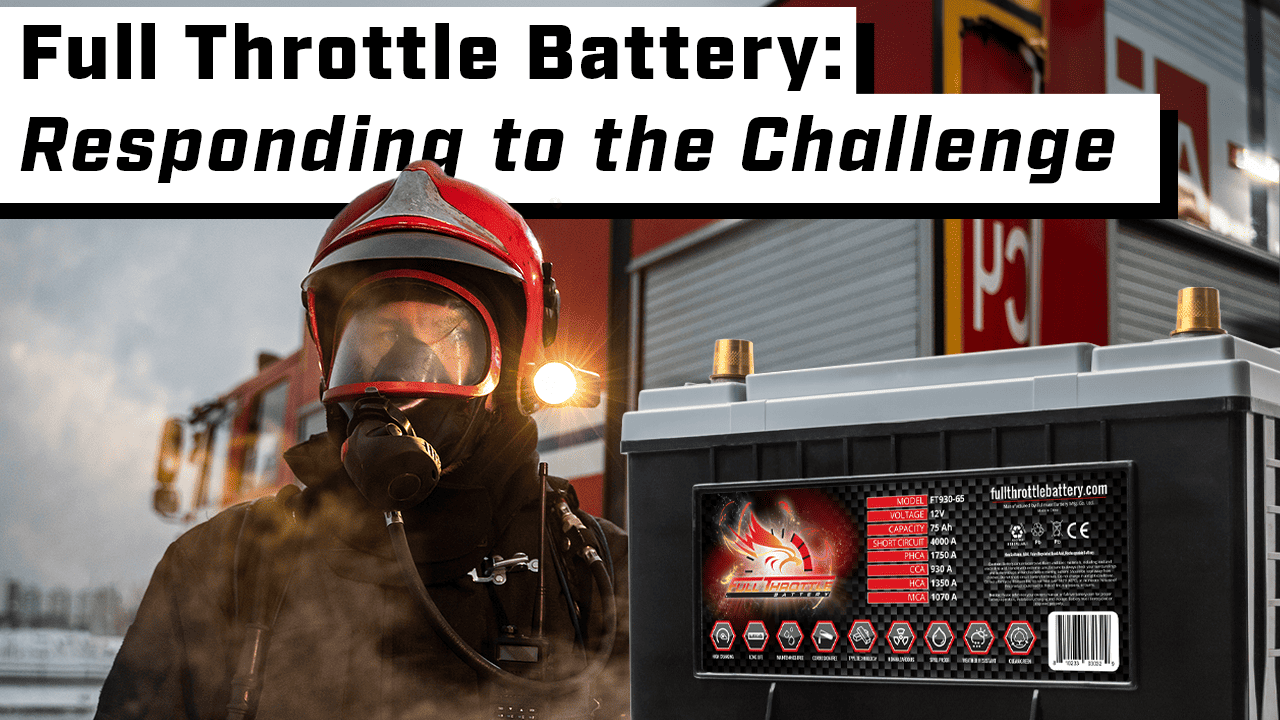
Built for Duty: Full Throttle Battery Supports Emergency Response
September 12, 2023
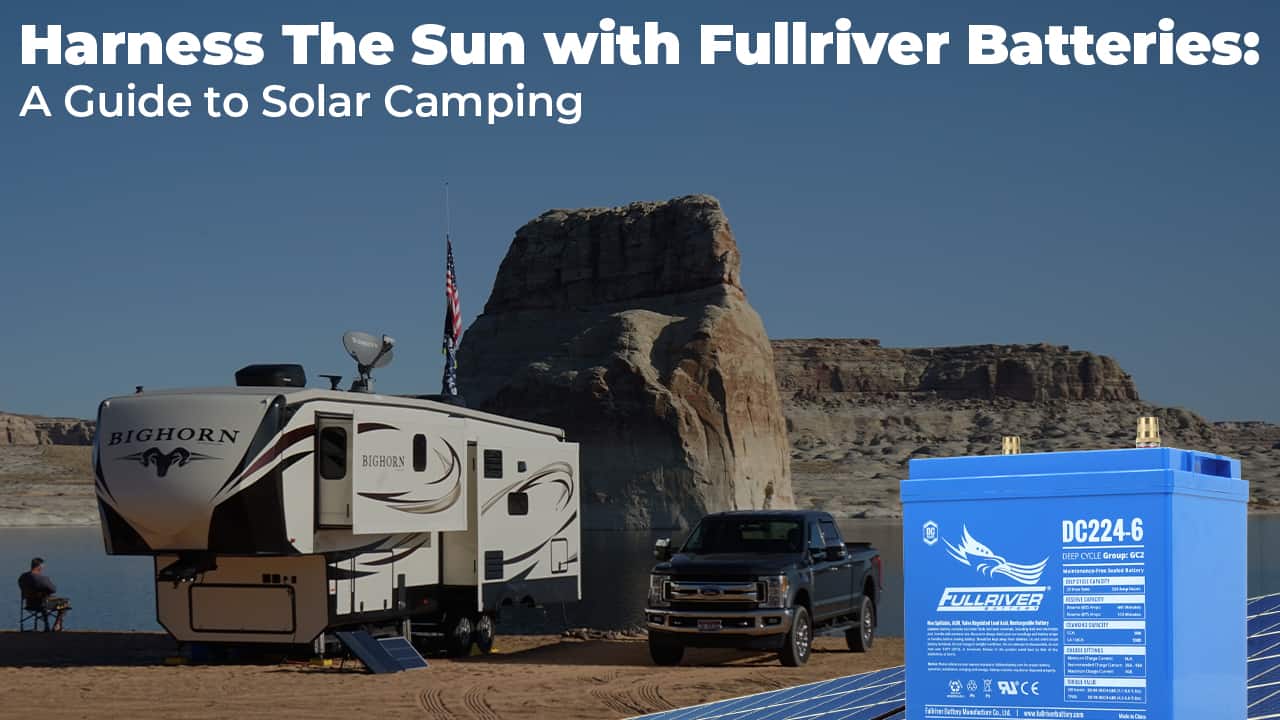
The Best Batteries for Camping
April 17, 2023
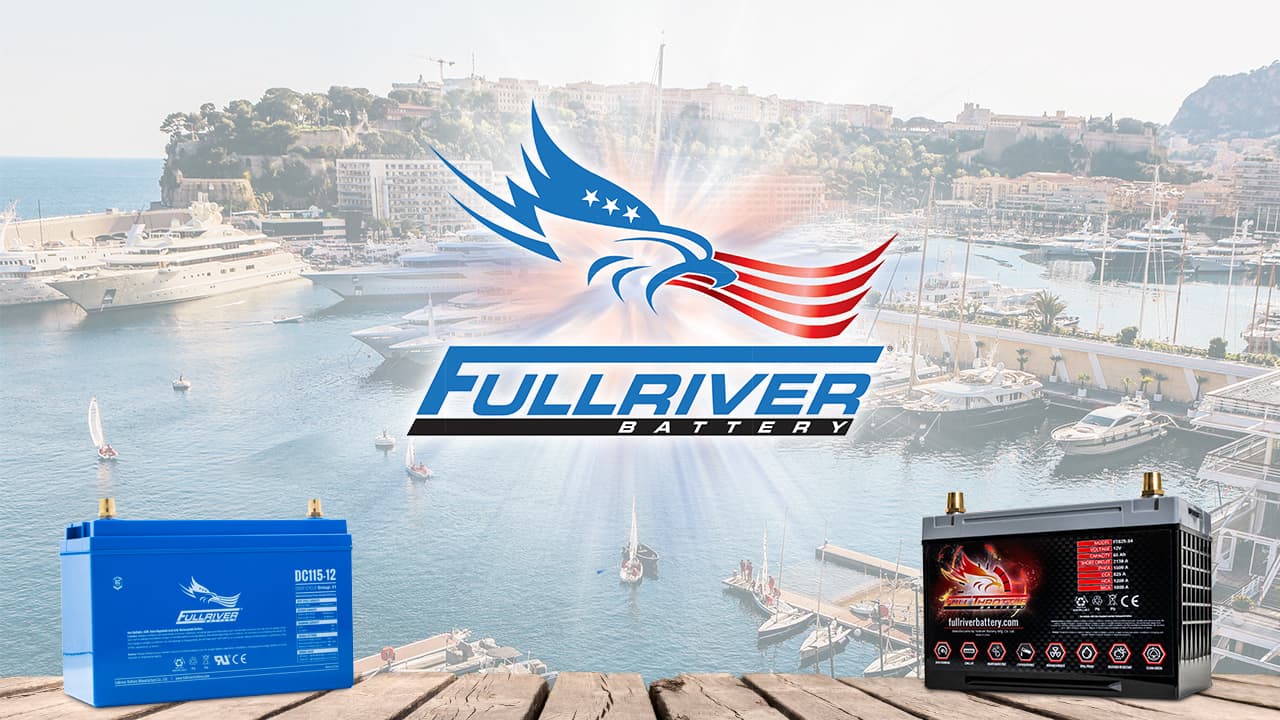
The Best Battery for Marine
March 22, 2023
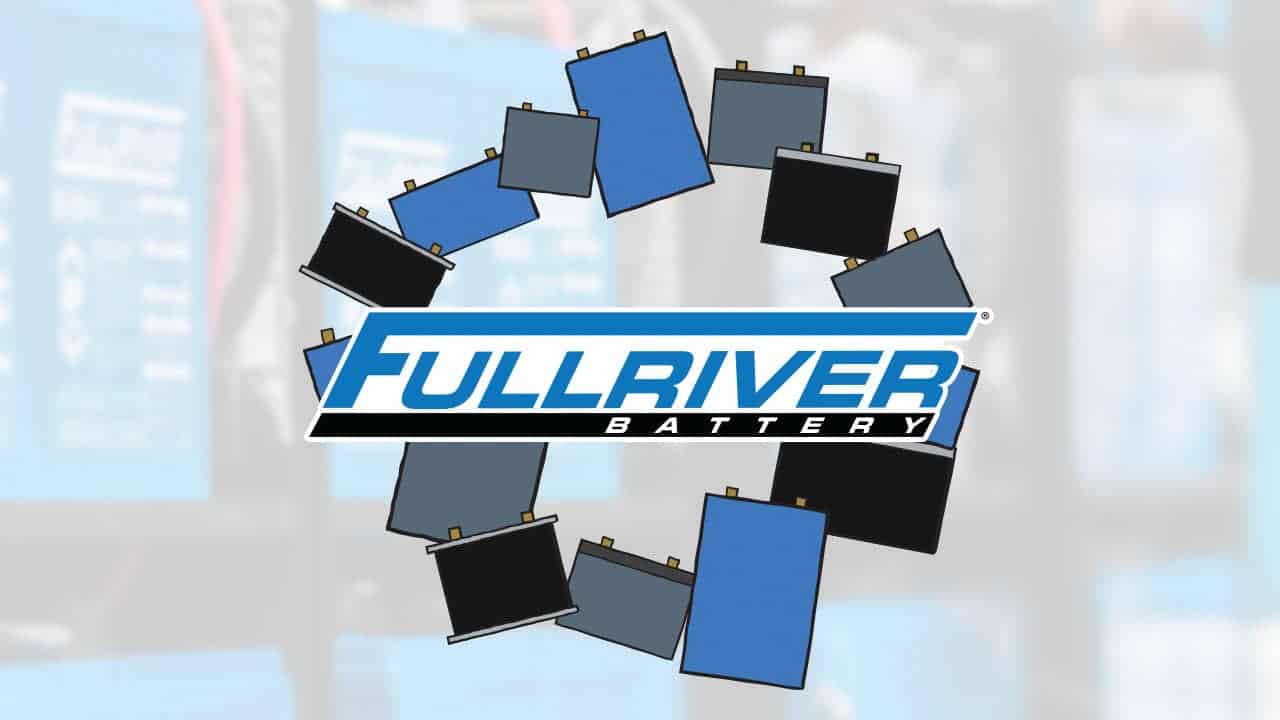
Top 3 Reasons AGM Batteries Excel: Tolerant, Resilient, Versatile
February 22, 2023
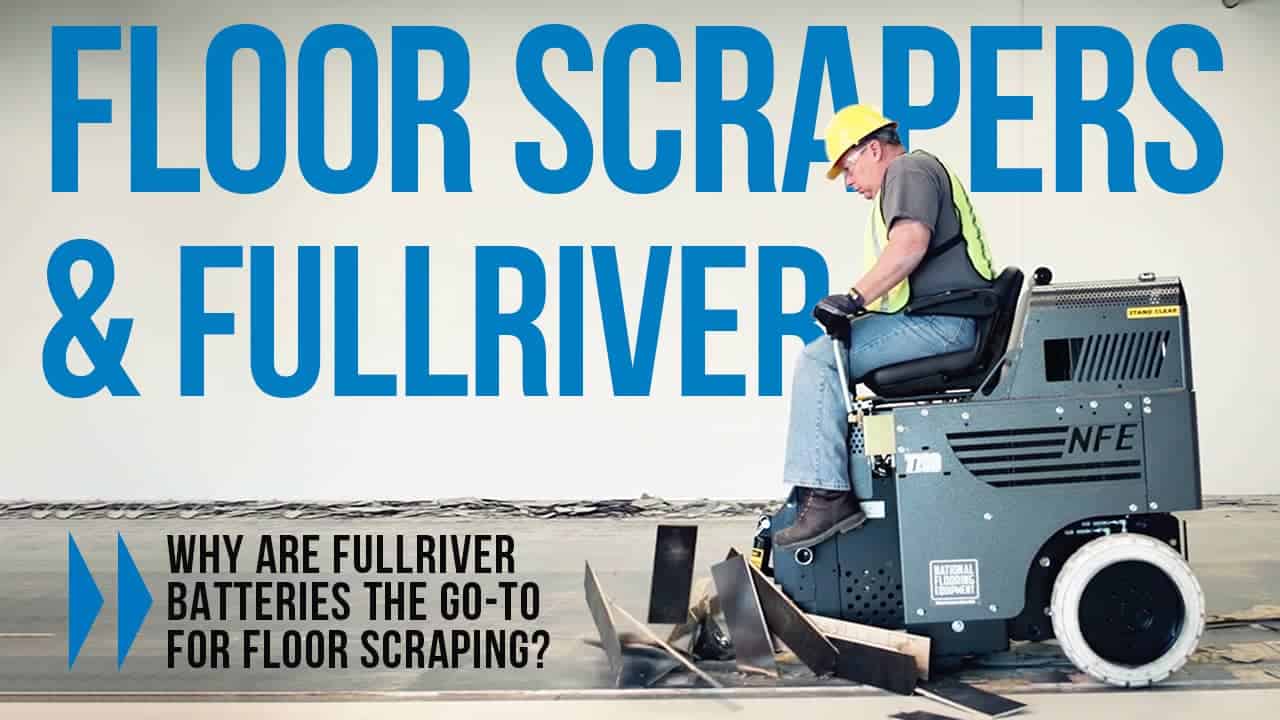
Why are Fullriver Batteries the Go-to for Floor Scraping?
November 29, 2022
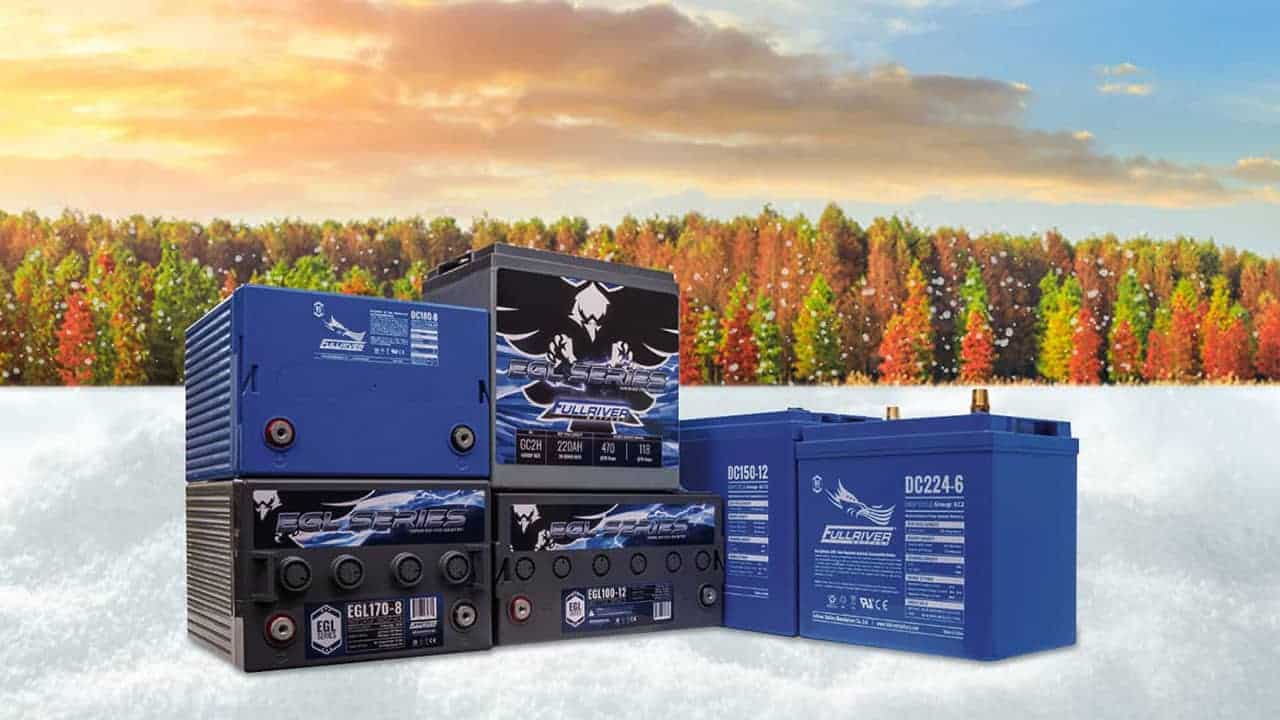
A Surprisingly Simple Winterizing Protocol
October 18, 2022
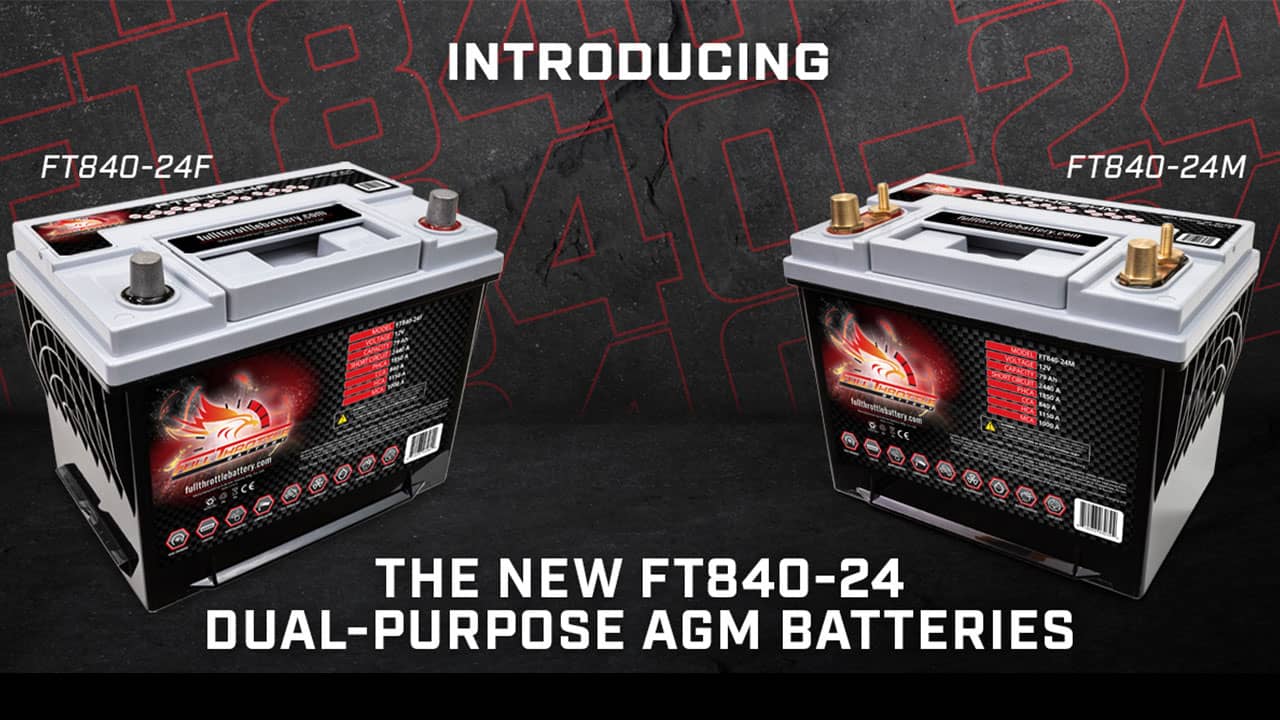
Full Throttle Presents: 24F and 24M
September 12, 2022
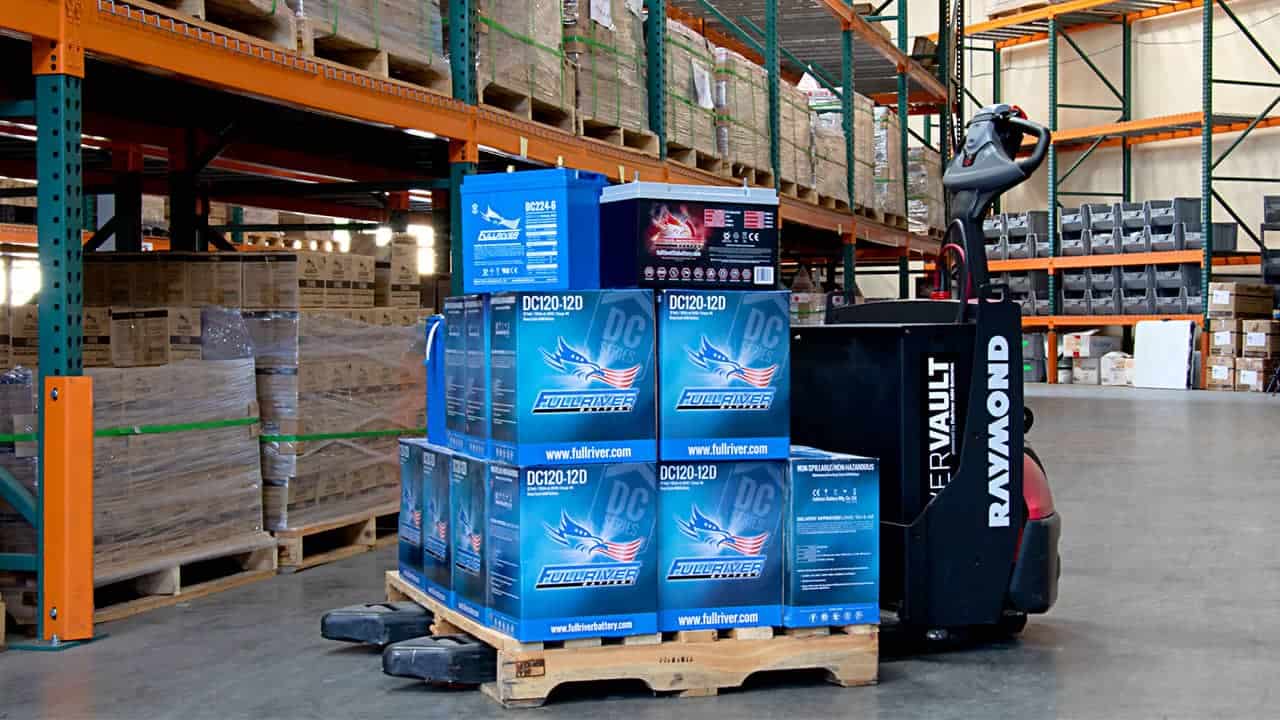
After Fifty Years, What’s Still so Great about AGM?
August 25, 2022
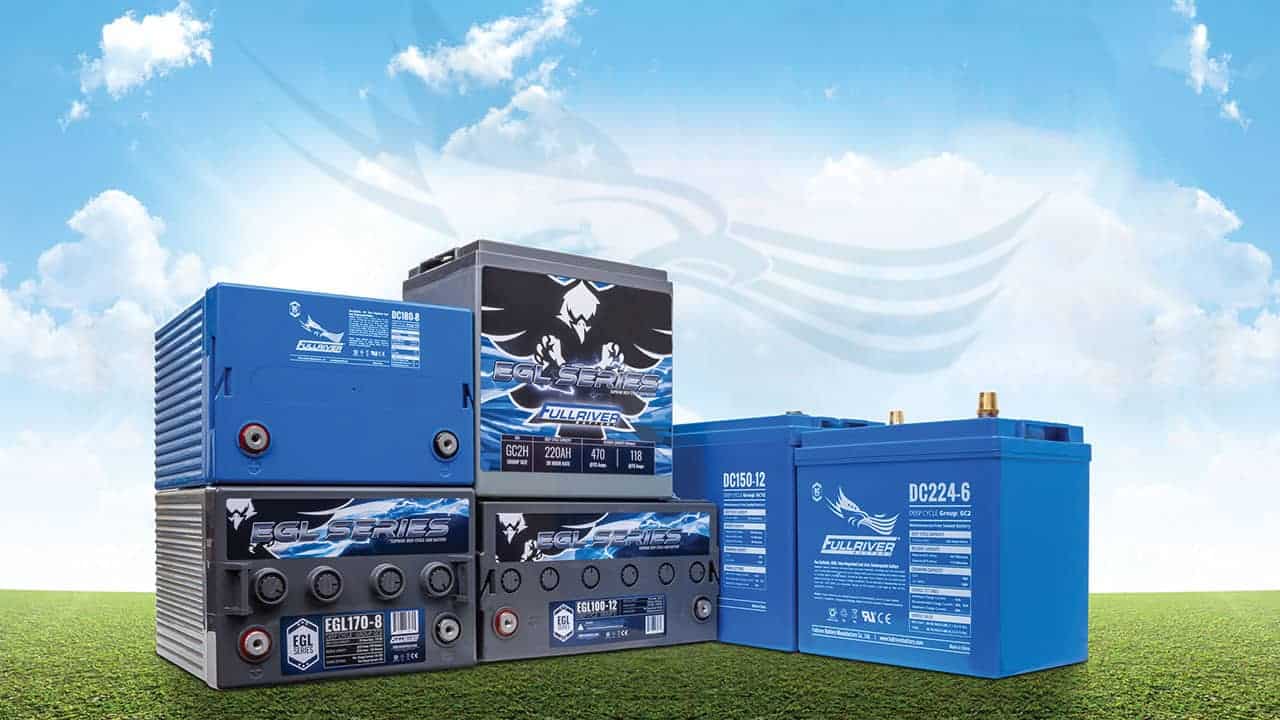
What is a True Deep Cycle Battery?
July 26, 2022
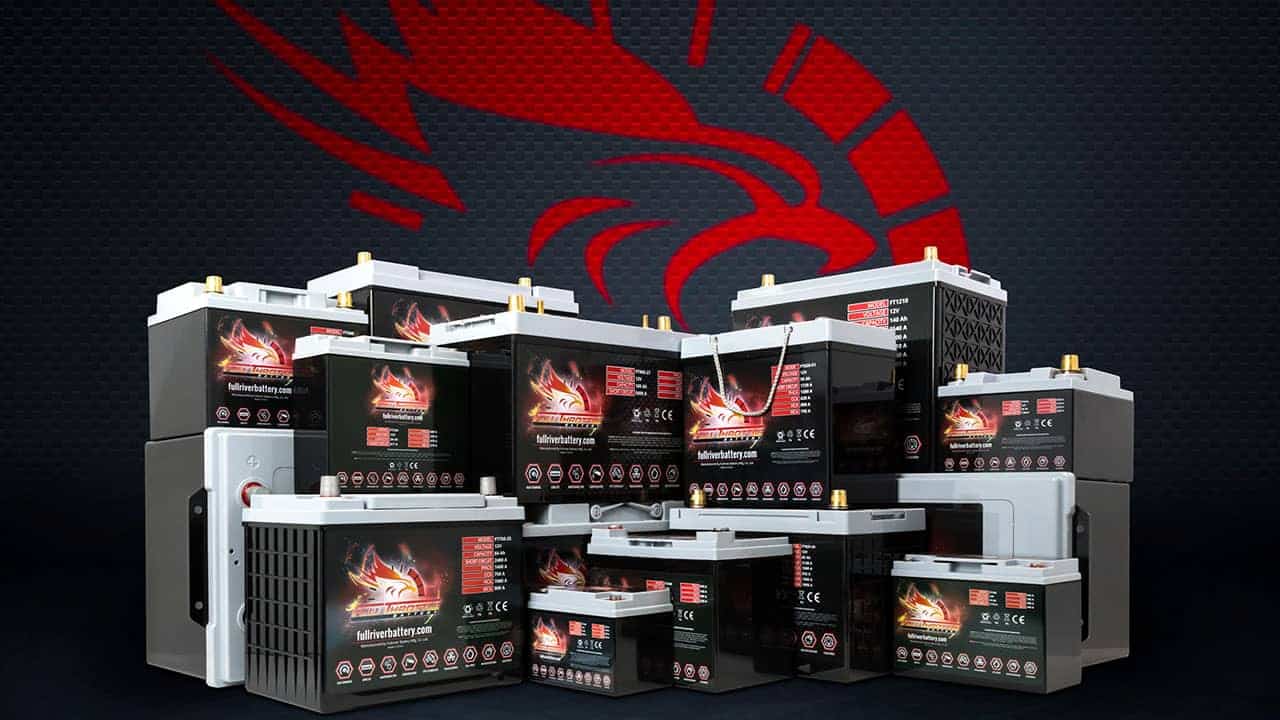
What is a dual-purpose Battery?
June 27, 2022
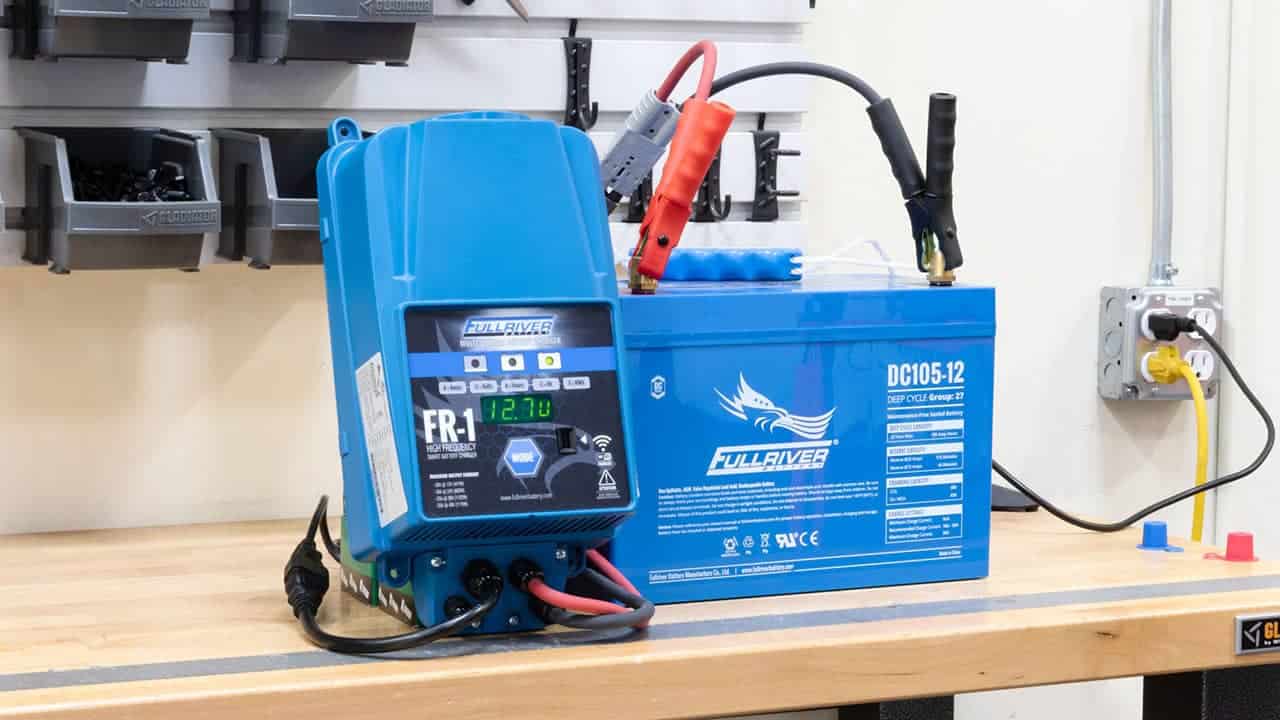
Do I need a special charger for an AGM battery?
May 24, 2022
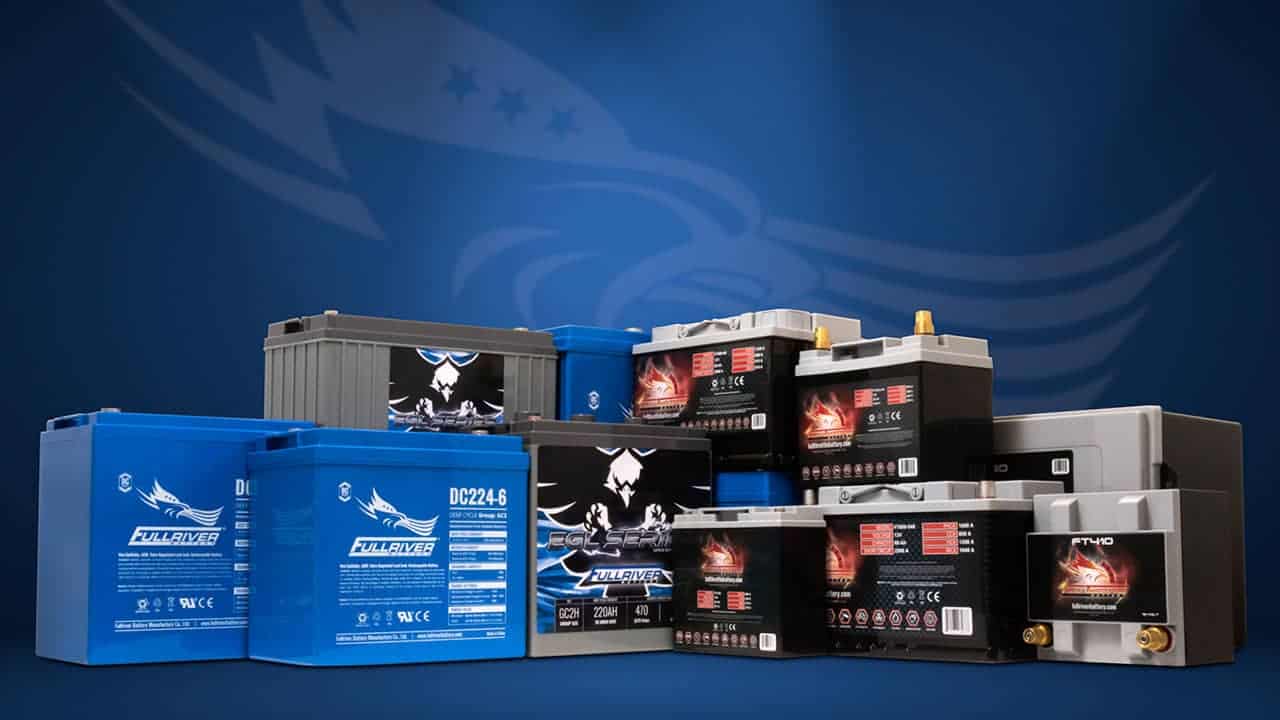
How long does a Fullriver AGM battery last?
April 26, 2022
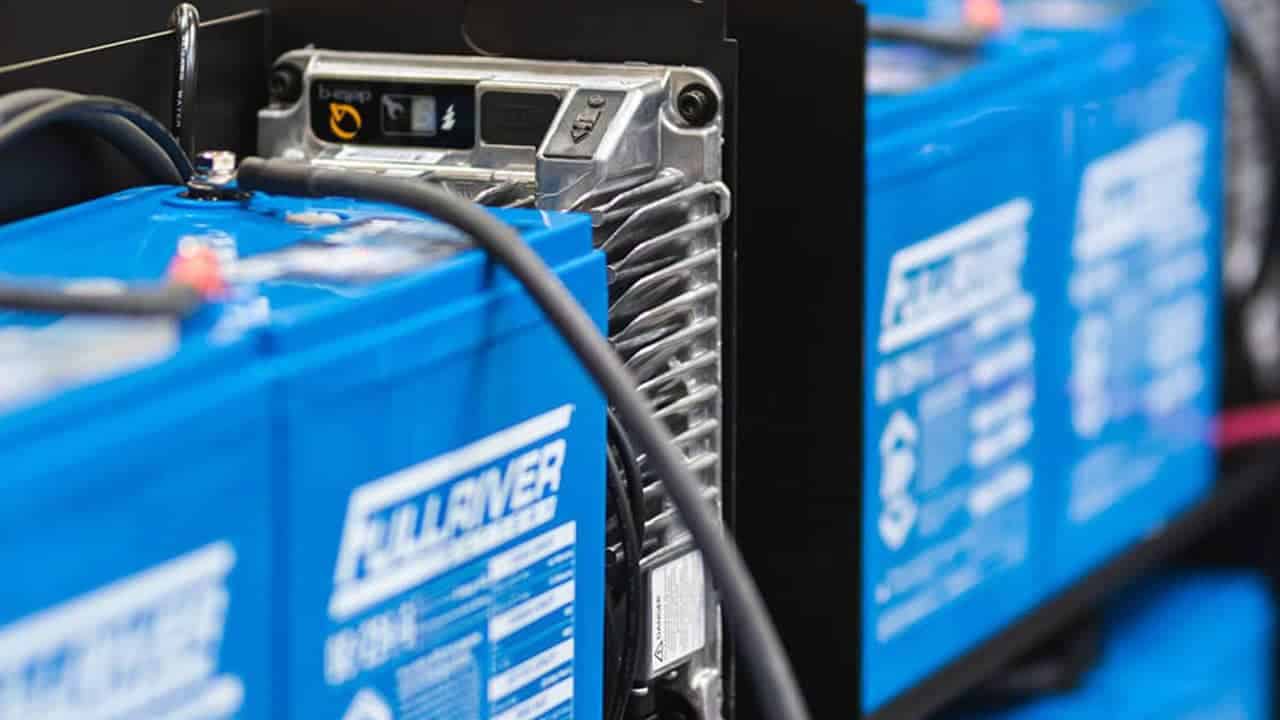
How fast can you charge an AGM Battery?
March 7, 2022
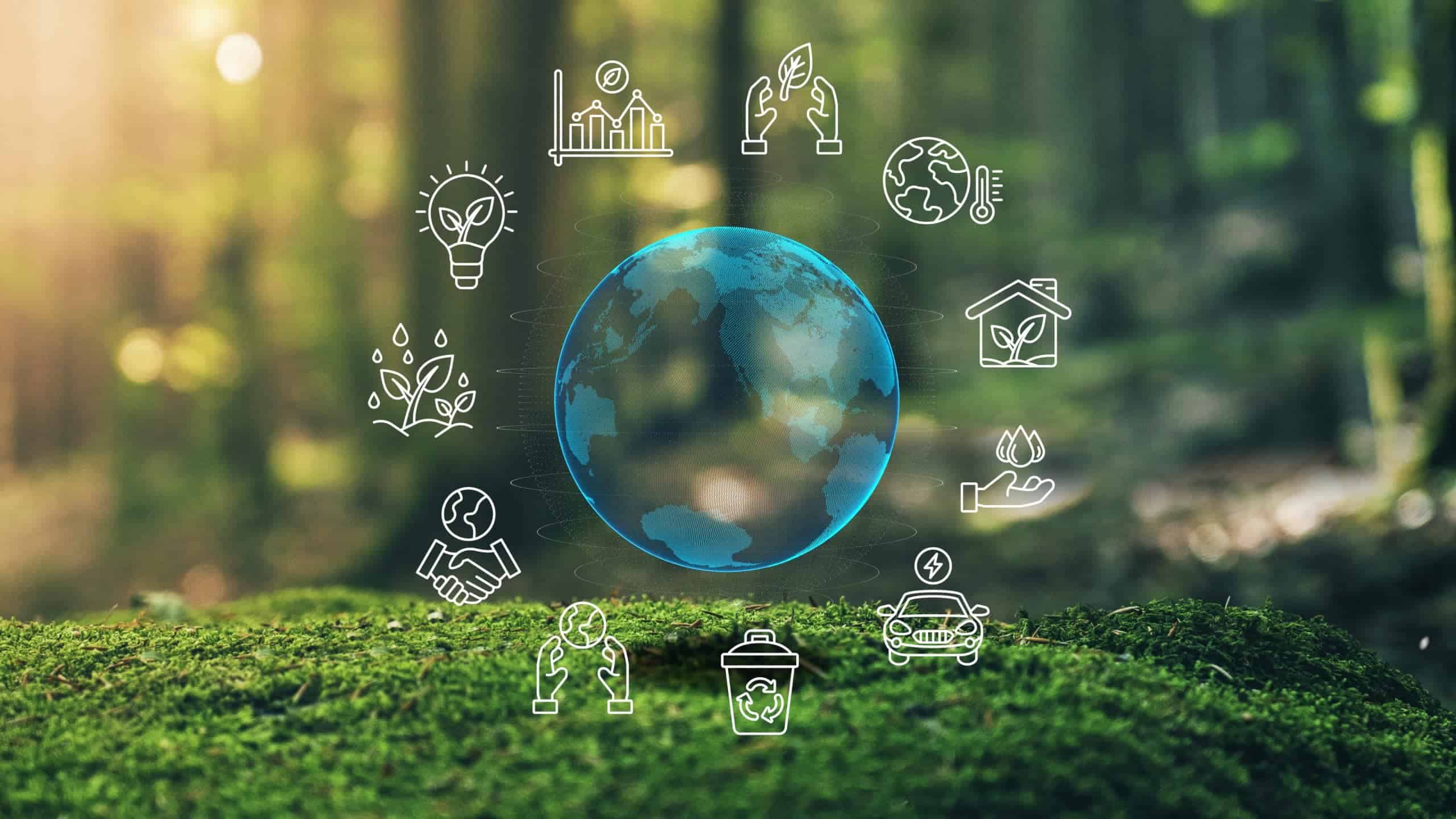
Sustainability, Reliability, or Both?
February 24, 2022
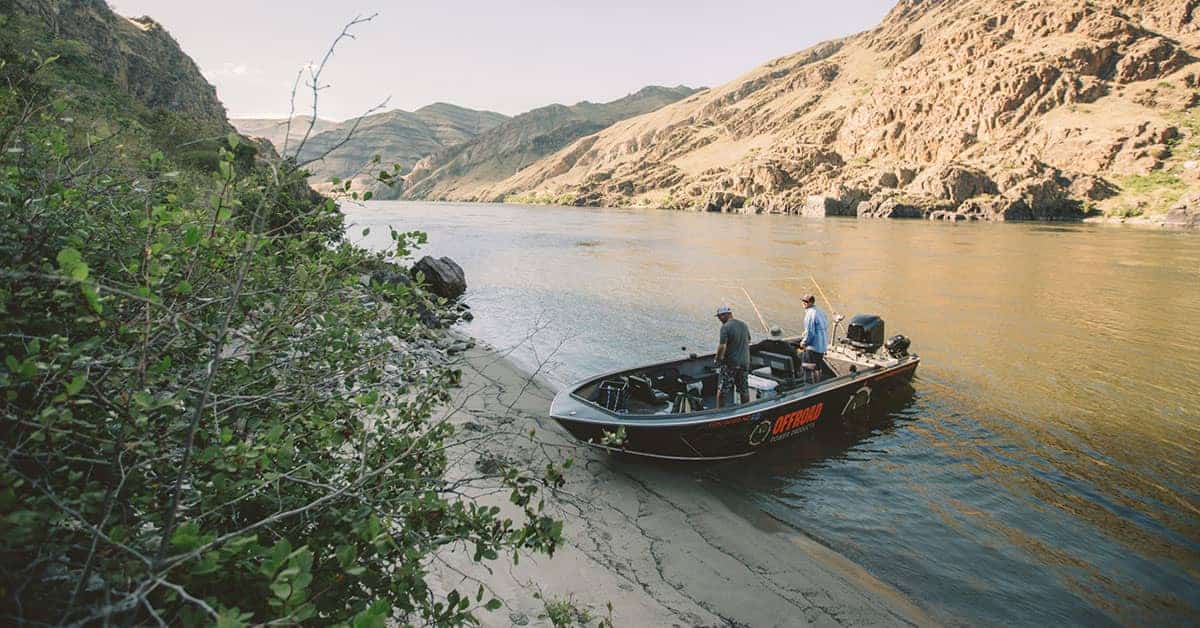
Make Sure Your Battery Isn’t An Anchor This Spring!
January 7, 2022
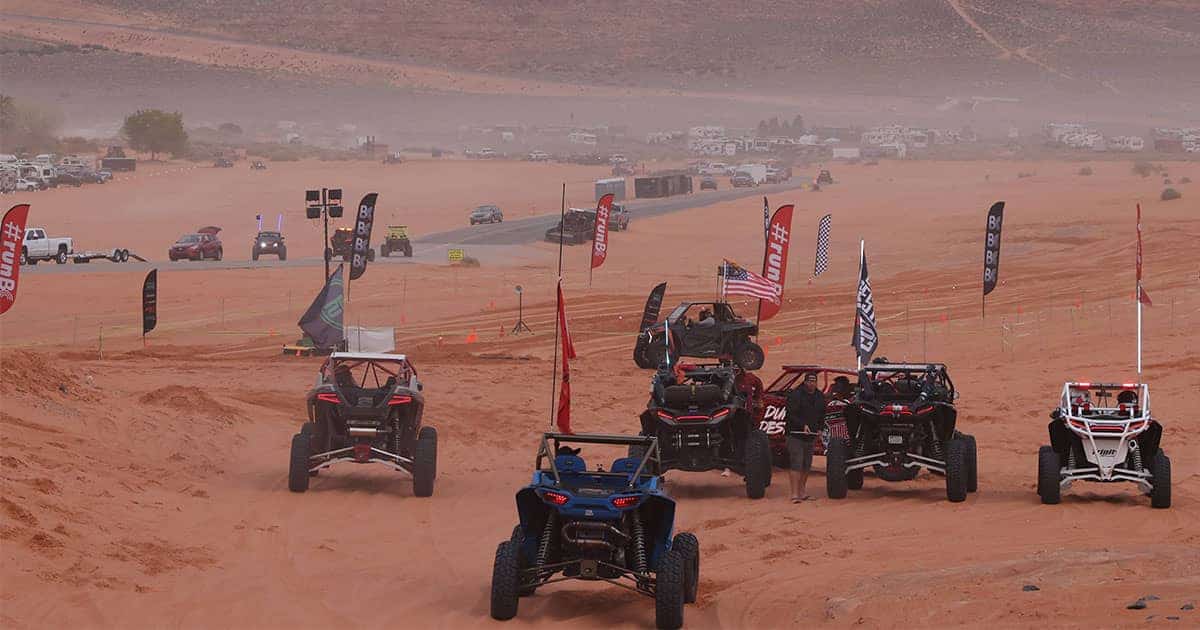
UTV Takeover Utah 2021 Recap
December 7, 2021
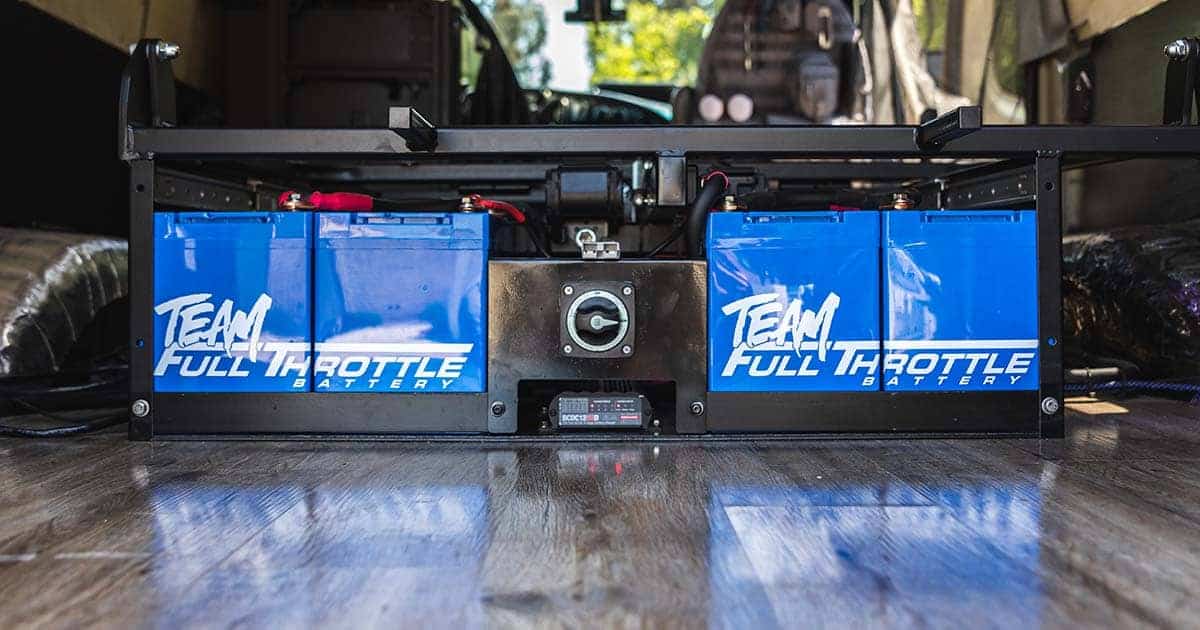
Vandeto’s Endless Power with REDARC and Fullriver Battery
August 30, 2021
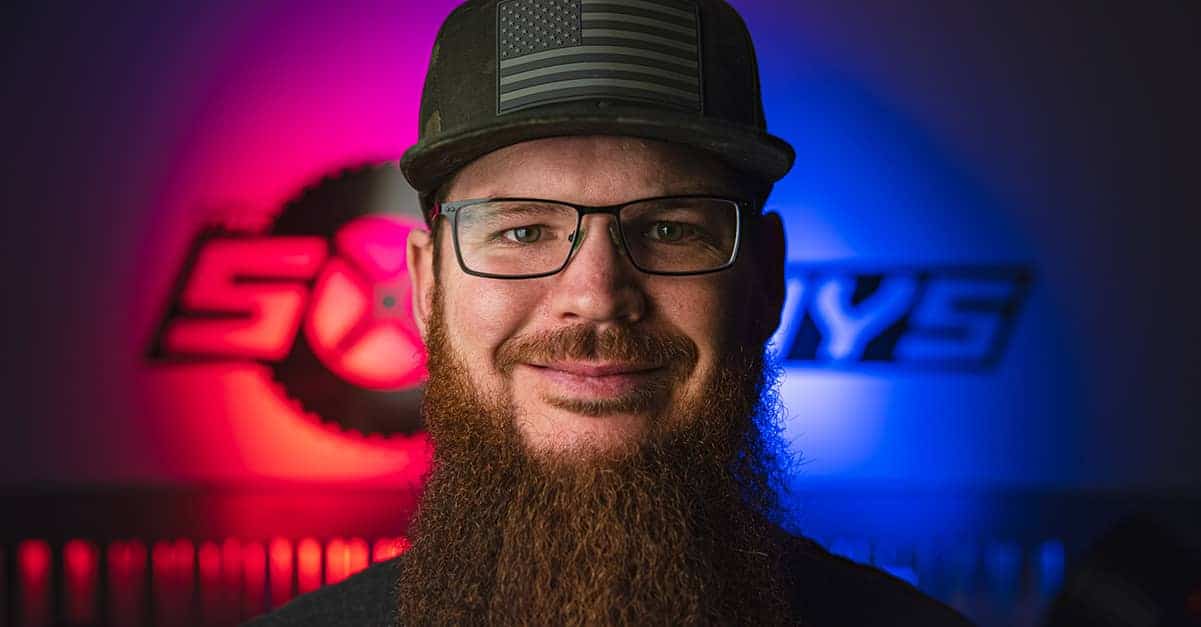
Not Just Another SxS Guy: Zach Jeffers
June 17, 2021
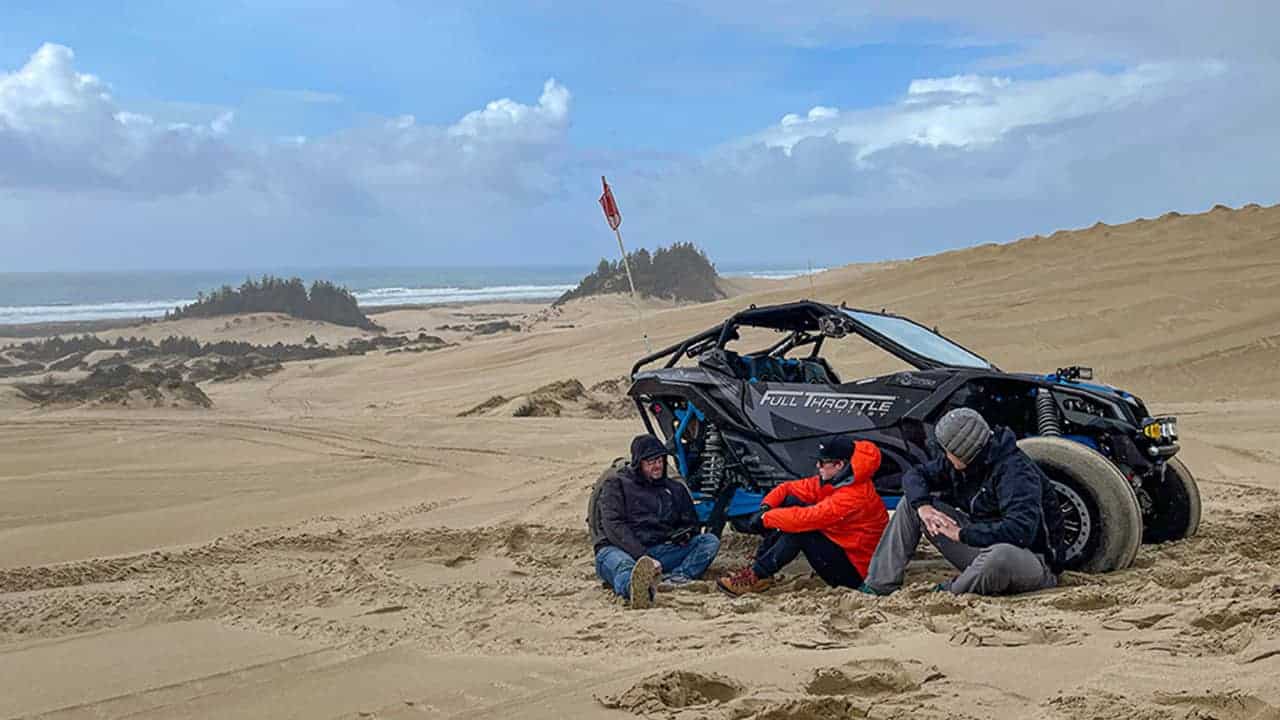
Full Throttle Battery Invades Winchester Bay
March 30, 2021
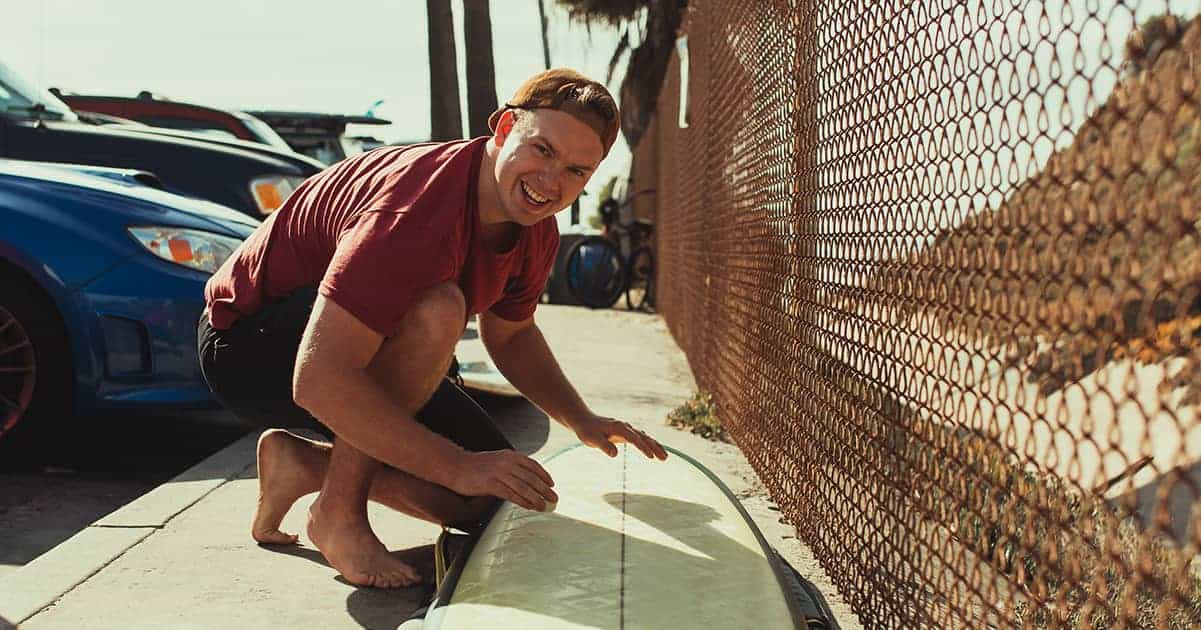
An Overland Explorer and Filmmaker: Cameron Hotchkiss
March 26, 2021
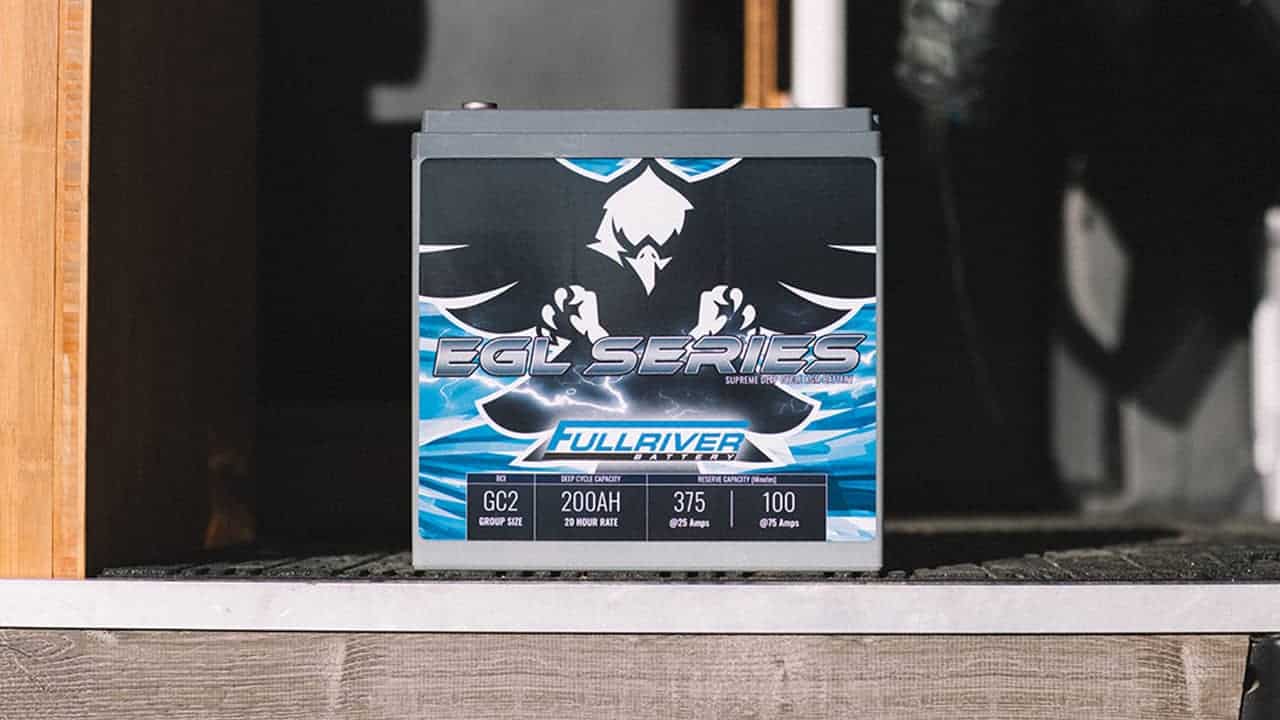
A New Battery with Double the Cycle Life – EGL Series
March 25, 2021